Polyester yarn and fiber have become fundamental materials in modern textile manufacturing, offering an unmatched combination of durability, versatility, and cost-effectiveness. As one of the most widely used synthetic fibers globally, polyester yarn and fiber continue to revolutionize industries ranging from fashion and home textiles to automotive and technical applications. This comprehensive guide explores the various types of polyester yarn and fiber, their unique characteristics, production processes, and extensive applications across multiple sectors.
Understanding Polyester Yarn and Fiber
Before diving into specific types, it’s essential to understand what makes polyester yarn and fiber so valuable. Polyester is a synthetic polymer made from purified terephthalic acid (PTA) and monoethylene glycol (MEG). Through polymerization and spinning processes, these raw materials transform into the durable fibers we know today.
Key Advantages of Polyester Yarn and Fiber:
- Exceptional strength and durability – Outperforms many natural fibers in tensile strength
- Wrinkle and shrink resistance – Maintains shape and appearance after repeated washing
- Quick-drying properties – Low moisture absorption makes it ideal for activewear
- Chemical and mildew resistance – Suitable for outdoor and industrial environments
- Excellent color retention – Holds dyes better than many natural fibers
- Cost-effective production – More affordable than many natural alternatives
These properties make polyester yarn and fiber indispensable across numerous applications, from everyday clothing to high-performance technical textiles.
Detailed Exploration of Polyester Yarn Types
1. Polyester Staple Fiber (PSF)
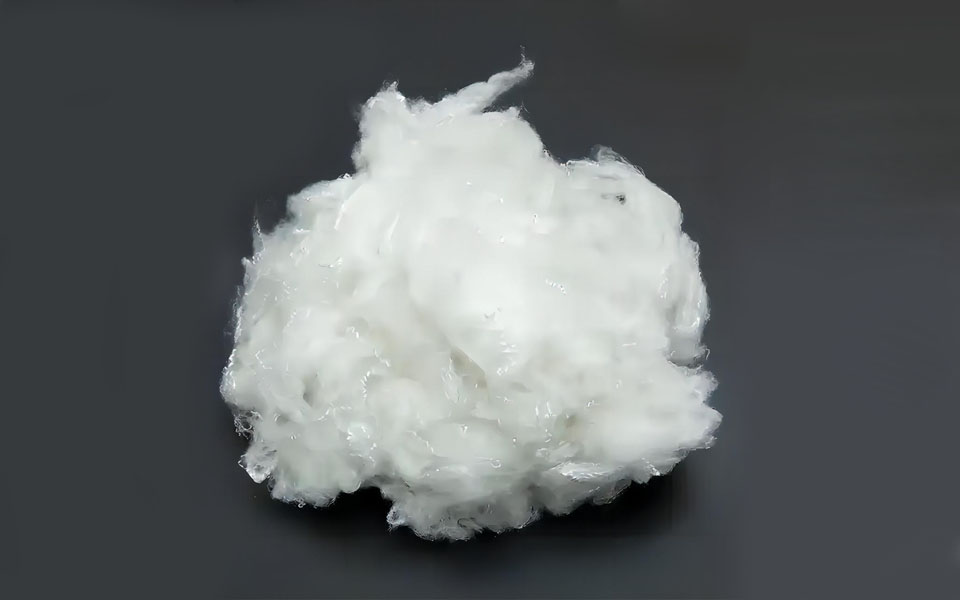
Polyester staple fiber (PSF) consists of short, discrete lengths of fiber that mimic natural fibers like cotton or wool. Typically ranging from 1.5 to 6 inches in length, PSF can be spun into yarns or used directly in non-woven applications.
Production Process:
- Polymerization of PTA and MEG
- Melt spinning to create continuous filaments
- Drawing and crimping for texture
- Cutting into staple lengths
- Baling for shipment
Technical Specifications:
- Denier range: 0.8D to 20D
- Tenacity: 3.5-7.0 g/d
- Elongation at break: 15-50%
- Melting point: 250-260°C
Advanced Applications:
- Automotive textiles: Seat covers, headliners, and trunk liners
- Geotextiles: Erosion control fabrics and road stabilization materials
- Filtration media: High-temperature filter bags for industrial applications
- Medical textiles: Surgical drapes and disposable medical fabrics
2. Partially Oriented Yarn (POY)
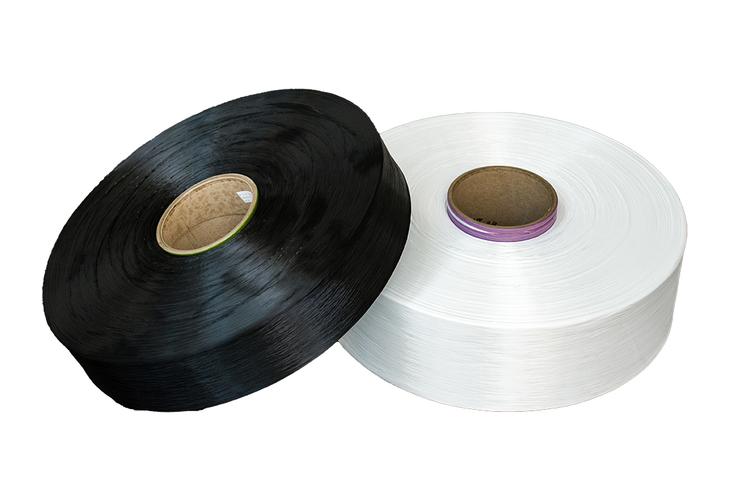
Partially Oriented Yarn (POY) represents an intermediate product in polyester yarn production, requiring additional processing to achieve its final properties.
Manufacturing Insights:
- Produced through high-speed spinning (2500-3500 m/min)
- Contains about 60-70% of final orientation
- Requires draw-texturing or drawing to become usable
Quality Parameters:
- Orientation: 50-70% of fully drawn yarn
- Tenacity: 1.8-2.5 g/d
- Elongation: 100-180%
- Uster evenness: <1.0%
Industrial Processing Options:
- Draw-texturing: Converts POY to DTY for stretch fabrics
- Warp-drawing: Produces FDY for high-strength applications
- Air-jet texturing: Creates bulkier yarns for special effects
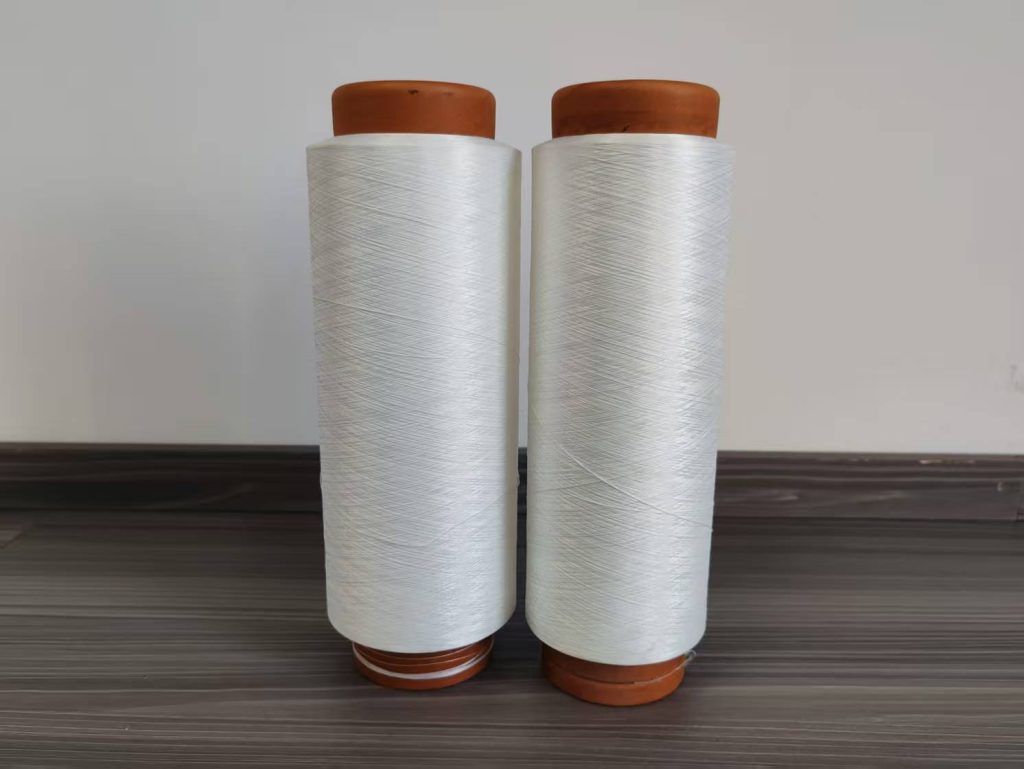
Draw Textured Yarn (DTY) offers exceptional elasticity and bulk, making it ideal for comfort-focused applications.
Texturing Technologies:
- False-twist texturing: Most common method using friction disks
- Air-jet texturing: Creates looped structure for special effects
- Knit-de-knit process: Produces crimped texture
Performance Characteristics:
- Elastic recovery: 90-95% after 10% stretch
- Bulkiness: 20-30% higher than flat yarns
- Pilling resistance: 4-5 on ICI pilling scale
- Dye uptake: 10-15% higher than flat yarns
Specialty Variants:
- Microfiber DTY: <1 denier per filament for ultra-soft fabrics
- Bright/Semi-dull DTY: Different luster levels for design flexibility
- Antimicrobial DTY: Treated with silver ions for hygiene applications
4. Fully Drawn Yarn (FDY)
Fully Drawn Yarn (FDY) represents the highest strength category of polyester yarns, with complete molecular orientation.
Production Excellence:
- Spin-draw process at 4000-6000 m/min
- Hot drawing at 180-220°C
- Relaxation for stability
Technical Superiority:
- Tenacity: 4.5-8.0 g/d
- Elongation: 15-30%
- Boil-off shrinkage: <3%
- Uster CV%: <0.8
High-Performance Uses:
- Tire cord: High-tenacity variants for radial tires
- Conveyor belts: Industrial strength requirements
- Sailcloth: Marine-grade durability
- Parachute fabric: Reliability in extreme conditions
Emerging Trends in Polyester Yarn Technology
The polyester yarn and fiber industry continues to evolve with technological advancements:
Sustainable Innovations:
- Recycled polyester (rPET): Made from post-consumer PET bottles
- Bio-based polyester: Using renewable feedstock
- Closed-loop production: Minimizing water and chemical use
Functional Enhancements:
- Phase-change materials: For temperature regulation
- Conductive fibers: Smart textile applications
- UV-resistant variants: For outdoor durability
Smart Manufacturing:
- Industry 4.0 integration: AI-driven quality control
- Digital twin technology: For process optimization
- Blockchain traceability: From raw material to finished product
Global Market Perspective
The polyester yarn and fiber market continues to show strong growth:
- Market size: $105 billion (2023)
- Projected CAGR: 5.8% (2024-2030)
- Leading producers: China (65% share), India, Southeast Asia
- Key growth drivers: Fast fashion, technical textiles, sustainability demands
Conclusion: The Future of Polyester Yarn and Fiber
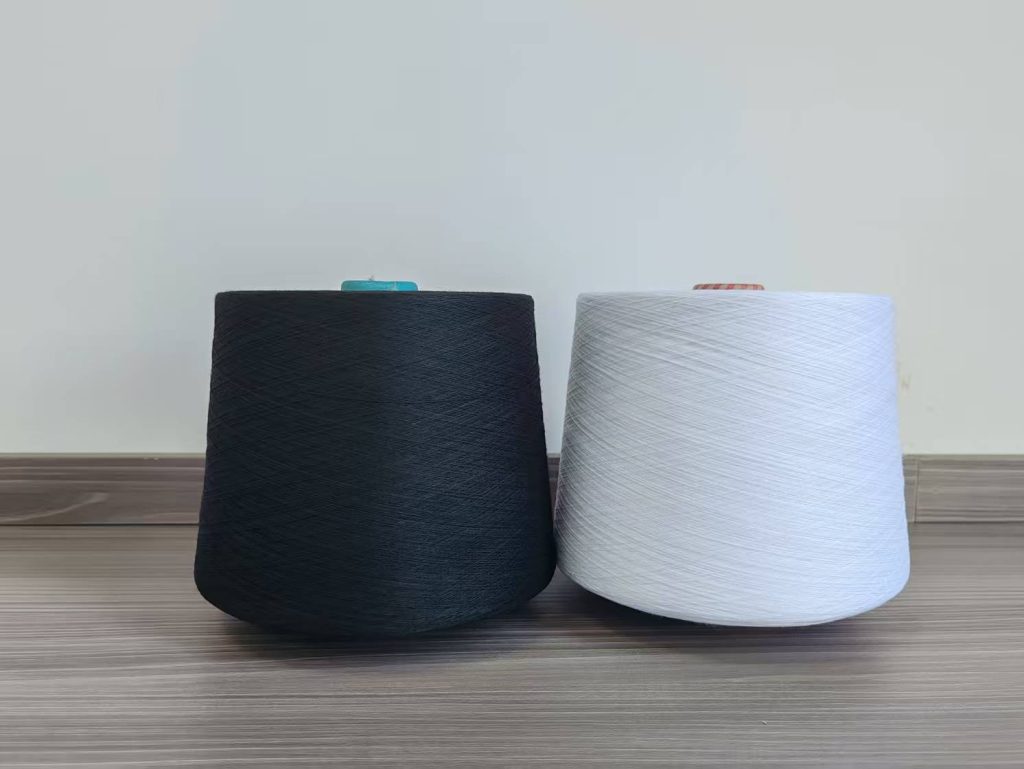
As we’ve explored throughout this guide, polyester yarn and fiber remain at the forefront of textile innovation. From basic apparel to cutting-edge technical applications, these versatile materials continue to adapt to market demands through:
- Enhanced sustainability with recycled and bio-based options
- Improved performance through advanced polymer engineering
- Smart functionality for the Internet of Textiles
- Cost-efficient production at scale
Manufacturers and designers who fully understand the capabilities of polyester yarn and fiber – from PSF to FDY and specialty variants – will be best positioned to capitalize on these opportunities in the evolving global textile landscape.
By Yarn